Introduction
Interior design is a beautiful balance of timeless tradition and contemporary innovation. Among the many patterns that have stood the test of time, herringbone tiles hold a special place. Recognized by their distinctive zigzag arrangement, herringbone tiles are experiencing a strong resurgence in modern interiors across Australia and around the world. Homeowners, architects, and designers are rediscovering this centuries-old pattern for its ability to bring movement, sophistication, and visual depth to a space. But what makes herringbone so enduring? To answer this, we need to take a closer look at its rich history, adaptability, and design appeal.
A Brief History of Herringbone
The herringbone pattern has a surprisingly ancient lineage. Its name is derived from the resemblance to the skeleton of a herring fish, but its use extends far beyond the sea-inspired imagery.
See more: The Benefits of Using Plywood Curved Concrete Forms in Custom Builds
- Roman Roots: The earliest examples of herringbone can be traced back to the Roman Empire, where it was used in road construction. Known as “opus spicatum,” Roman engineers laid bricks and stones in herringbone formations to create strong, durable roads. The interlocking pattern helped absorb pressure from heavy foot traffic, horses, and carts, ensuring longevity.
- Medieval and Renaissance Europe: The herringbone motif transitioned from roads to interiors, particularly in wooden parquet flooring. By the 16th century, French châteaux and Italian villas showcased elegant herringbone floors, turning the pattern into a symbol of luxury and refinement.
- Global Spread: Over the centuries, herringbone became a hallmark of European architecture and gradually spread worldwide. By the 20th century, it had found its way into tilework, fabrics, and even textiles, proving its adaptability across mediums.
This deep historical foundation makes herringbone more than just a design trend—it’s a cultural and architectural legacy.
Why Herringbone is Back in Style
So why, after centuries, is herringbone seeing a modern comeback? Several factors contribute to its revived popularity:
- Timeless Appeal – The pattern is instantly recognizable, carrying both heritage and elegance. It works beautifully in both classic and modern interiors.
- Versatility – Herringbone can be used in flooring, walls, backsplashes, and outdoor areas. It seamlessly blends with a variety of design styles, from minimalistic Scandinavian to luxurious contemporary.
- Texture and Movement – Unlike linear or grid-like patterns, herringbone introduces a sense of movement. It guides the eye across the room, creating visual interest without overwhelming the space.
- Adaptability to Modern Materials – Today’s herringbone tiles come in an array of finishes—ceramic, porcelain, marble, or wood-look—making them more accessible and affordable than ever.
In Australia, where open-plan living and natural light are design staples, herringbone tiles are valued for the way they add depth and dimension without cluttering a space.
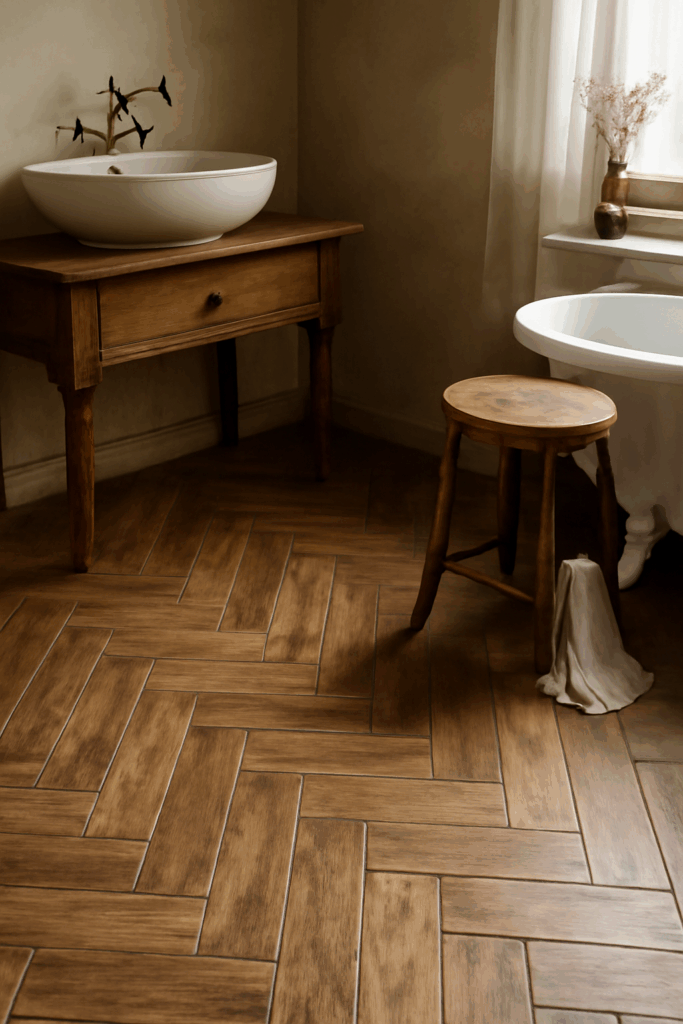
Design Applications
Herringbone tiles are no longer confined to flooring. They are being used creatively across the home, making them a designer’s favorite tool.
- Bathrooms: A herringbone tiled shower wall or floor instantly elevates the space, adding a spa-like quality. Light-colored marble or porcelain in a herringbone arrangement creates a serene and timeless look.
- Kitchens: One of the most popular applications is the kitchen backsplash. A herringbone layout transforms even the simplest subway tiles into a design statement. It pairs beautifully with stone benchtops and metallic fixtures.
- Living Areas: Timber-look herringbone tiles or parquet floors bring warmth and sophistication to open living spaces. They can serve as a focal point while remaining subtle enough to complement other design elements.
- Outdoor Areas: Stone or porcelain herringbone tiles work wonderfully on patios and walkways, providing both durability and visual charm.
This flexibility allows homeowners to use herringbone in small accents or bold, large-scale designs, depending on their vision.
Materials and Finishes
One reason herringbone remains so popular is the wide variety of materials available today:
- Ceramic Tiles – Affordable and easy to maintain, ceramic herringbone tiles are perfect for kitchens and bathrooms.
- Porcelain Tiles – Durable and versatile, porcelain is ideal for both indoor and outdoor applications.
- Marble Tiles – Luxurious and elegant, marble herringbone tiles add a touch of classic sophistication, though they require more upkeep.
- Wood-Look Tiles – For those who love timber flooring but want durability, porcelain wood-look herringbone tiles are a popular choice.
- Glass Tiles – Often used in backsplashes, glass herringbone tiles can add a reflective, modern touch to kitchens and bathrooms.
Each finish influences the final atmosphere of the room, from rustic charm to sleek modernism.
Pros and Cons of Herringbone Tiles
Like any design choice, herringbone tiles have their strengths and challenges.
Pros:
- Timeless and stylish, ensuring designs won’t look outdated quickly.
- Adds visual texture and movement.
- Increases perceived value of a home, appealing to buyers.
- Works across many design styles, from traditional to modern.
Cons:
- Installation can be labor-intensive and costly compared to simple layouts.
- Requires precision; mistakes in alignment are noticeable.
- Can generate more tile waste due to the angled cuts.
For many homeowners, the investment is worth it, given the elegance and sophistication herringbone brings to a space.
Styling Tips
To get the most out of herringbone tiles, consider these expert tips:
- Choose Contrasting Grout: Dark grout with light tiles (or vice versa) emphasizes the pattern, making it bold and eye-catching.
- Go Subtle with Tone-on-Tone: Using similar tones for tiles and grout creates a seamless, sophisticated look.
- Play with Orientation: Horizontal herringbone elongates a room, while vertical layouts add height and drama.
- Mix Finishes: Combine matte and glossy tiles to introduce depth and dimension.
- Balance with Simplicity: Because herringbone is visually striking, pair it with simpler design elements to avoid overwhelming the space.
Future of Herringbone in Interior Design
The enduring popularity of herringbone suggests it’s far from a passing trend. As sustainable building materials and new tile technologies emerge, herringbone will likely evolve further. Expect to see:
- Larger-format herringbone tiles for open spaces.
- Eco-friendly materials like recycled glass and sustainable ceramics.
- Creative hybrid designs combining herringbone with chevron or basketweave patterns.
- More use of bold colors and textured finishes in modern homes.
The pattern’s adaptability ensures that herringbone will continue to inspire future generations of designers and homeowners.
Conclusion
Herringbone tiles are more than just a stylish choice—they’re a piece of history reimagined for the modern world. From Roman roads to today’s Australian kitchens and bathrooms, this timeless pattern has continuously adapted while retaining its elegance and charm. Its versatility, visual movement, and ability to blend tradition with innovation make it a staple in interior design.
For anyone considering a renovation or new build, herringbone tiles offer the perfect balance of sophistication and durability. Whether used as a subtle detail or a bold statement, they embody the idea that true design classics never go out of style.